Warning
You are reading an old version of this documentation. If you want up-to-date information, please have a look at 2025.09 .Standard hoppers
The standard hoppers sold by Asyril include:
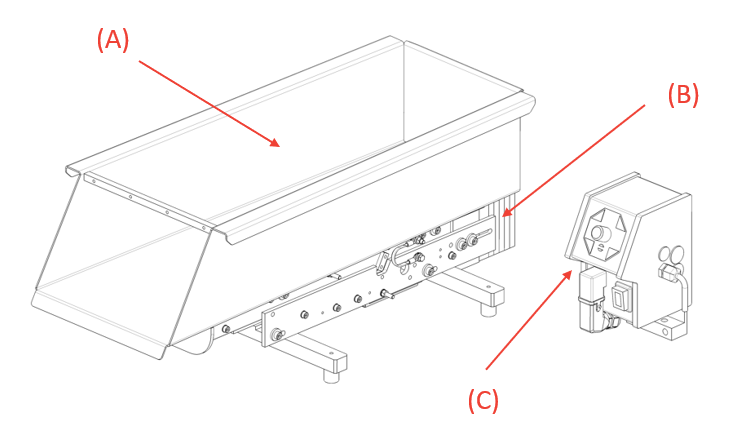
Fig. 56 Standard hoppers for Asycube 240, 380 and 530, including control unit
(A) The container (see Mechanical interfaces) receiving the parts. Depending on the size of the parts to be fed and the required machine autonomy, different sizes may be used (1L, 2L, 3L, 10L or 15L). These containers are in stainless steel Inox 1.4301.
(B) The linear vibrator (see Mechanical interfaces) that moves the parts on the container to feed the Asycube.
(C) The Control Unit used to adjust the hopper vibration amplitude.
A set of three different cables is also included (see Electrical interfaces).
Quick start instructions
Remove contents from box:
1x hopper unit
1x hopper control unit
3x cables (mains power cable, actuator power cable, digital control cable)
Install and mount the hopper, see more details in Mounting.
Install the hopper control unit, see more details in Mounting.
Connect the digital control cable from the Asycube digital output port to the hopper control unit.
Connect the actuator power cable from the hopper to the hopper control unit.
Connect to mains, either 115V or 230V and 50Hz or 60Hz.
Important
The input voltage and frequency must match the voltage and frequency of the hopper vibrating mechanism. If this is not respected, the hopper could be irreversibly damaged.
Turn the hopper control unit ON/OFF switch to ON.
Enable the digital output of the Asycube.
Confirm that the hopper is vibrating.
Adjust the vibration level as needed with the potentiometer (0-100%) on the hopper control unit.
Electrical interfaces
Wiring diagram
The hopper is supplied with the controller and cables ready to be installed. The Table 8 gives the current ratings for the different type of hoppers.
Important
The input voltage and frequency must match the voltage and frequency of the hopper vibrating mechanism. If this is not respected, the hopper could be irreversibly damaged.
Hopper type |
AC characteristics |
Actuator nominal current |
Recommended rated current |
---|---|---|---|
1L Hopper |
115VAC/50 or 60Hz |
0.17A |
1A 1 |
230VAC/50 or 60Hz |
0.08A |
1A 1 |
|
2L/3L Hopper |
115VAC/50 or 60Hz |
1.32A |
2A 1 |
230VAC/50 or 60Hz |
0.6A |
2A 1 |
|
10L/15L Hopper |
115VAC/50 or 60Hz |
1.32A |
2A 1 |
230VAC/50 or 60Hz |
0.6A |
2A 1 |
The cables length supplied with the hopper and the wiring diagram are shown in Fig. 57. The signal polarity of the controller cable is detailed in Table 9.
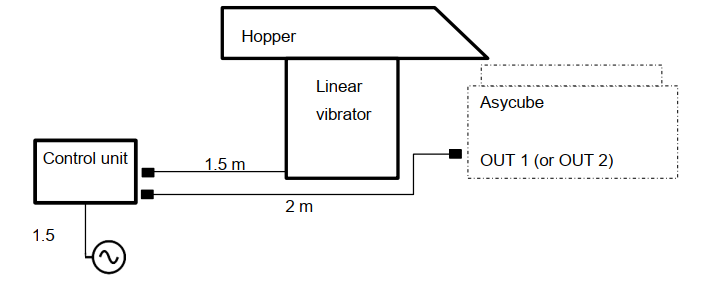
Fig. 57 Wiring diagram and cables length
Number |
Signal |
Internal wires |
Hopper control unit cable |
---|---|---|---|
1 |
L |
Labeled 1 or brown |
|
2 |
N |
Labeled 2 or blue |
|
3 |
PE |
Ground (green/yellow) |
Control Unit
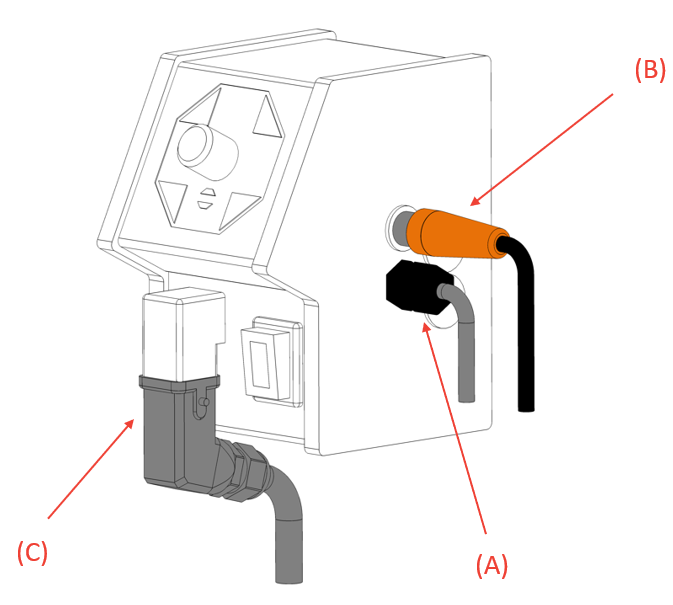
Fig. 58 Control unit
(A) Actuator power cable: connects the hopper controller to the linear vibrator.
(B) Digital control cable: connects the hopper controller to the Asycube.
(C) Mains power cable: connects the hopper controller to the mains supply.
The dimensions of the control unit including the supplied mounting bracket are detailed in Fig. 59.
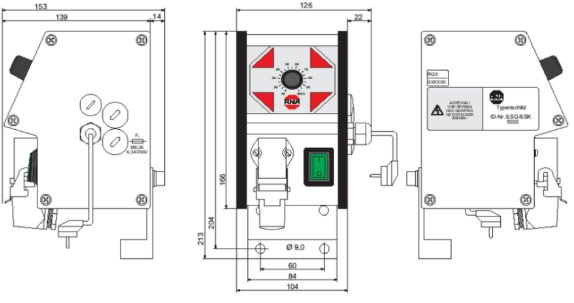
Fig. 59 Control unit
Note
Position the control unit so that you can reach the potentiometer.
Mechanical interfaces
The different variants of hoppers (1L, 2L, 3L, 10L and 15L) can be mounted on the back or on the side of the Asycube. This enables applications such as multi-feeding where multiple different parts are being fed onto the same Asycube simultaneously via multiple hoppers, as illustrated in Fig. 60.
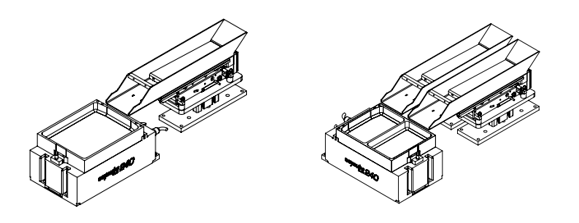
Fig. 60 Illustration of single part feeding versus multi-feeding with two parts
Note
With multi-feeding applications, since both parts will share the same vibration settings, attention must be paid to how parts are combined. A very heavy and large part combined with a light and small one might not give satisfying results. Since many factors can affect the vibration characteristics, we strongly advise you to perform some preliminary tests first.
The table below summarizes which hopper size can be used in conjunction with which Asycube with single part feeding or multi-feeding applications:
1L Hopper |
2L Hopper |
3L Hopper |
10L Hopper |
15L Hopper |
|
---|---|---|---|---|---|
Asycube 240 |
yes |
yes |
yes |
N/A |
N/A |
Asycube 380 |
yes |
yes |
yes |
yes |
yes 1 |
Asycube 530 |
yes |
yes |
yes |
yes |
yes |
1L Hopper |
2L Hopper |
3L Hopper |
10L Hopper |
15L Hopper |
|
---|---|---|---|---|---|
Asycube 240 |
yes |
N/A |
N/A |
N/A |
N/A |
Asycube 380 |
yes |
yes |
yes |
yes 2 |
N/A |
Asycube 530 |
yes |
yes |
yes |
yes 2 |
yes 2 |
Note
2L and 3L Hoppers are delivered with mounting feet which can be fastened to the machine base directly at the right height for an Asycube 240 using four M8x20 screws.
Note
When pairing 1L, 2L, 3L, 10L and 15L hoppers with Asycube 380 and Asycube 530, the optional modular hopper fixing kit allows the hopper to be mounted at the ideal height.
Note
When two hoppers can be mounted on the same long side of the Asycube, a multi-feeding application with up to 4 parts can also be considered by mounting 4 hoppers symmetrically. If your application requires a configuration with more than two hoppers, please visit the multi-feeding section in EYE+ documentation or contact our support team from our website.
The following diagrams represent at which height the different hoppers shall be mounted and the position of the holes to fix the hopper to the machine base plate for single part feeding and multi-feeding with two parts.
1 L hopper
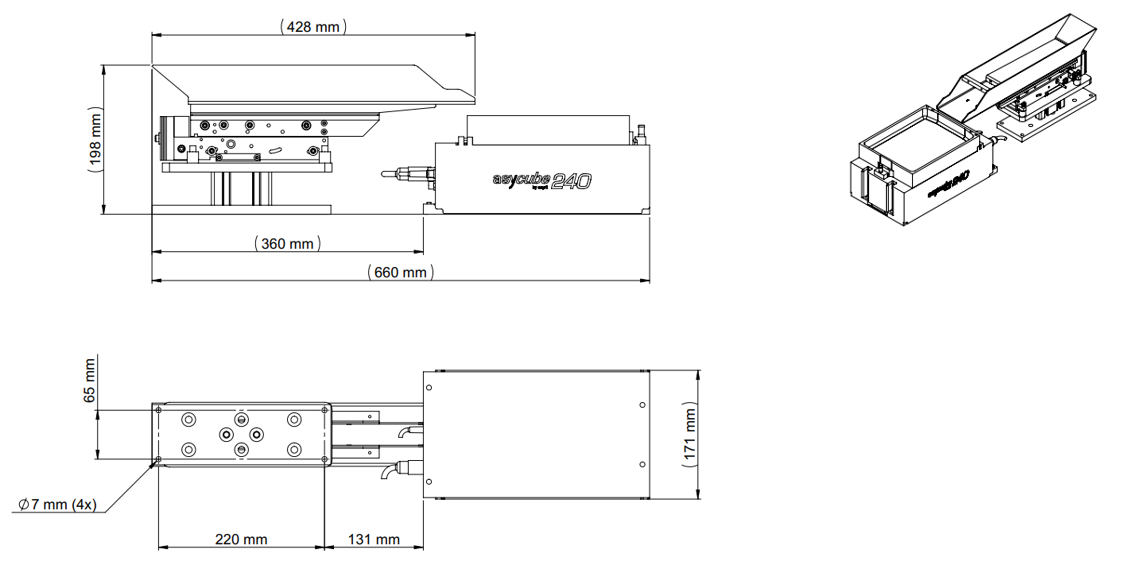
Fig. 61 Single part feeding: Asycube 240 with 1 L hopper
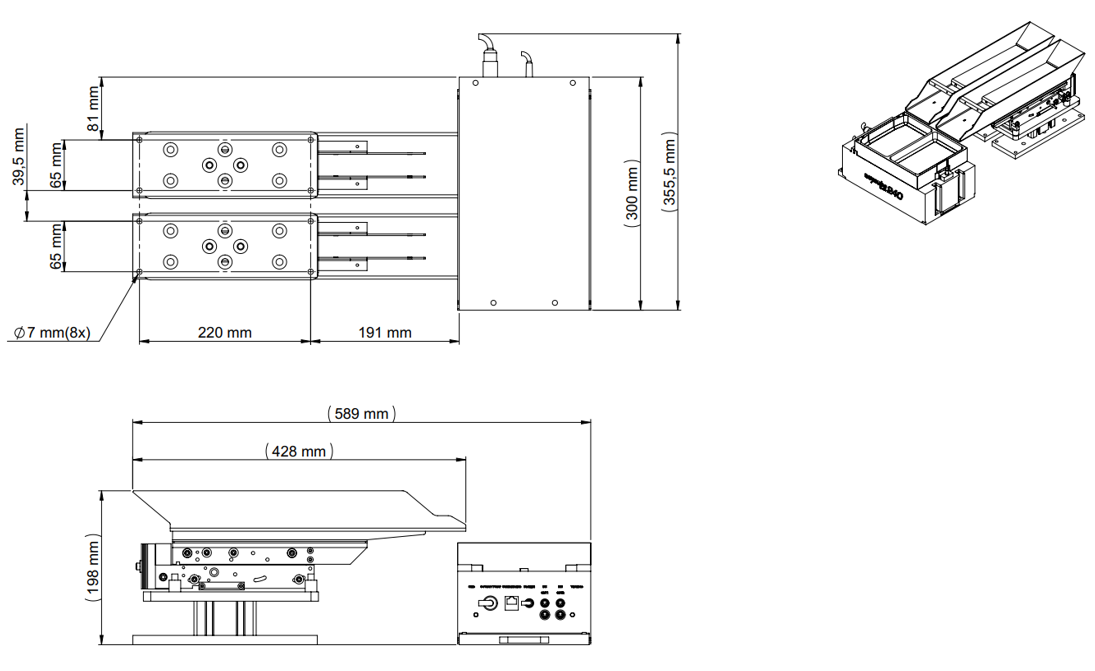
Fig. 62 Multi-feeding with two parts: Asycube 240 with two 1 L hoppers
2 L hopper
3 L hopper mechanical interfaces
10 L hopper mechanical interfaces
15 L hopper mechanical interfaces
Modular fixing kit
Tip
This section only concerns only the Asycube 380/530.
The modular fixing kit allows to position the hopper at a height perfectly adapted to the Asycube 380/530. The assembly instructions are explained below:
Step 1
Choose the fixation height and fasten the first half with 2x M5 screws
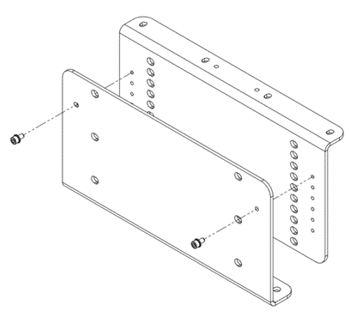
Note
The fixing kit height can be adjusted from 180 to 255 mm in steps of 15 mm
Step 2
Secure by fastening the 4x M8 screws with nuts
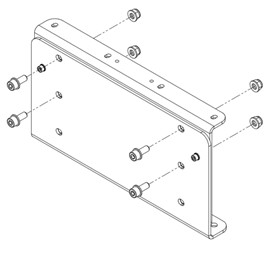
Step 3
Repeat Step 1 and 2 for the second half
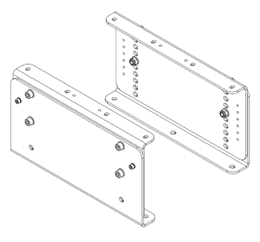
Step 4
Fasten the modular fixing kit on the machine base plate and then fix the hopper onto it
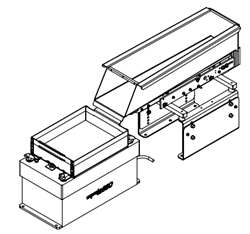