Warning
You are reading an old version of this documentation. If you want up-to-date information, please have a look at 2025.09 .Sequences and smart actions
Here are presented all the available commands that can be sent to the Asycube for the sequences and smart actions. These commands can be sent via Terminal or from your robot/PLC through Asycube’s Ethernet port (TCP/IP).
The above commands introduce parameters specific to smart actions that are described below.
Center of mass parameters for smart centering
When using the smart centering action EC or a sequence ES that includes a smart centering action, the center of mass of the parts on the platform must be filled in. As shown in Fig. 117, the positions on the platform are normalized between -1 and +1 in both directions in order to be independent of the resolution of the camera or of the choice of the camera manufacturer image orientation and origin. In the example below, the center of mass of the parts is located at coordinates (-0.5;0.7).
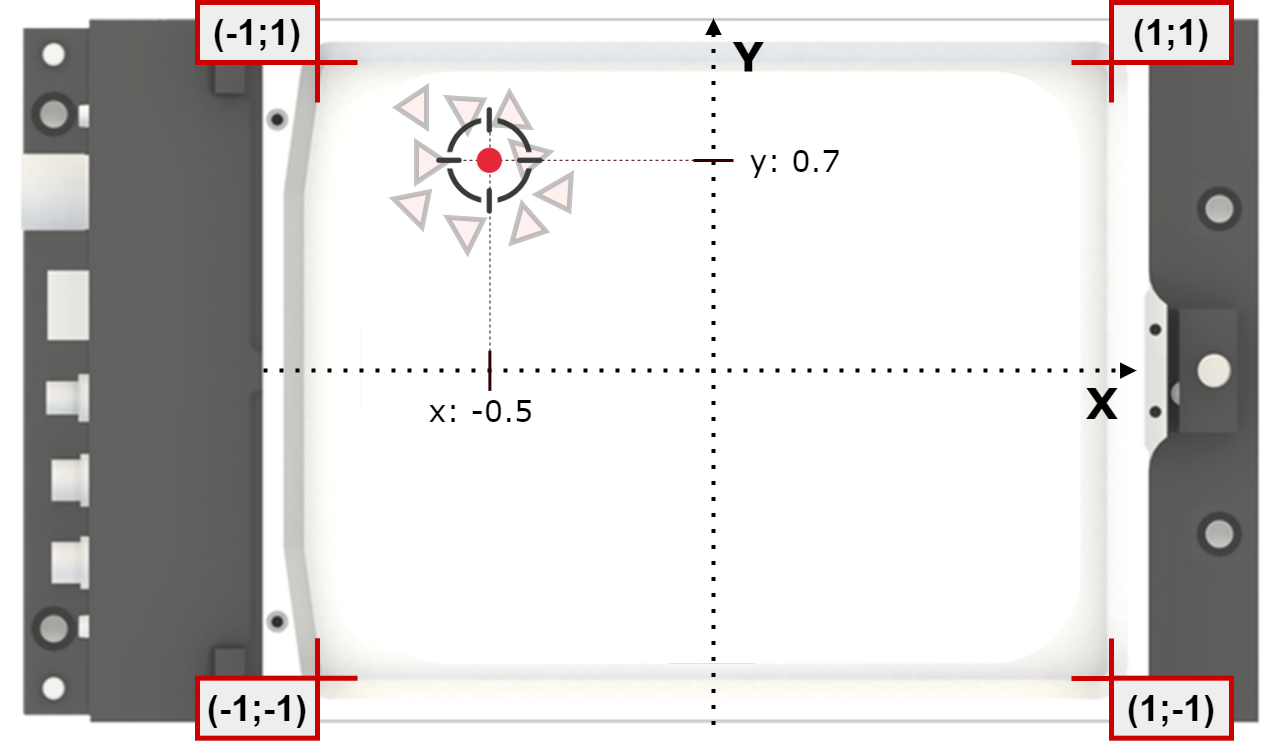
Fig. 117 Center of mass of parts - Platform normalized between -1 and +1
Platform division for smart centering
The smart centering action EC uses the center of mass coordinates given as parameters to select the most appropriate type of vibration and optimize the duration of the vibration. The vibration type is selected based on the platform division shown in Fig. 118.
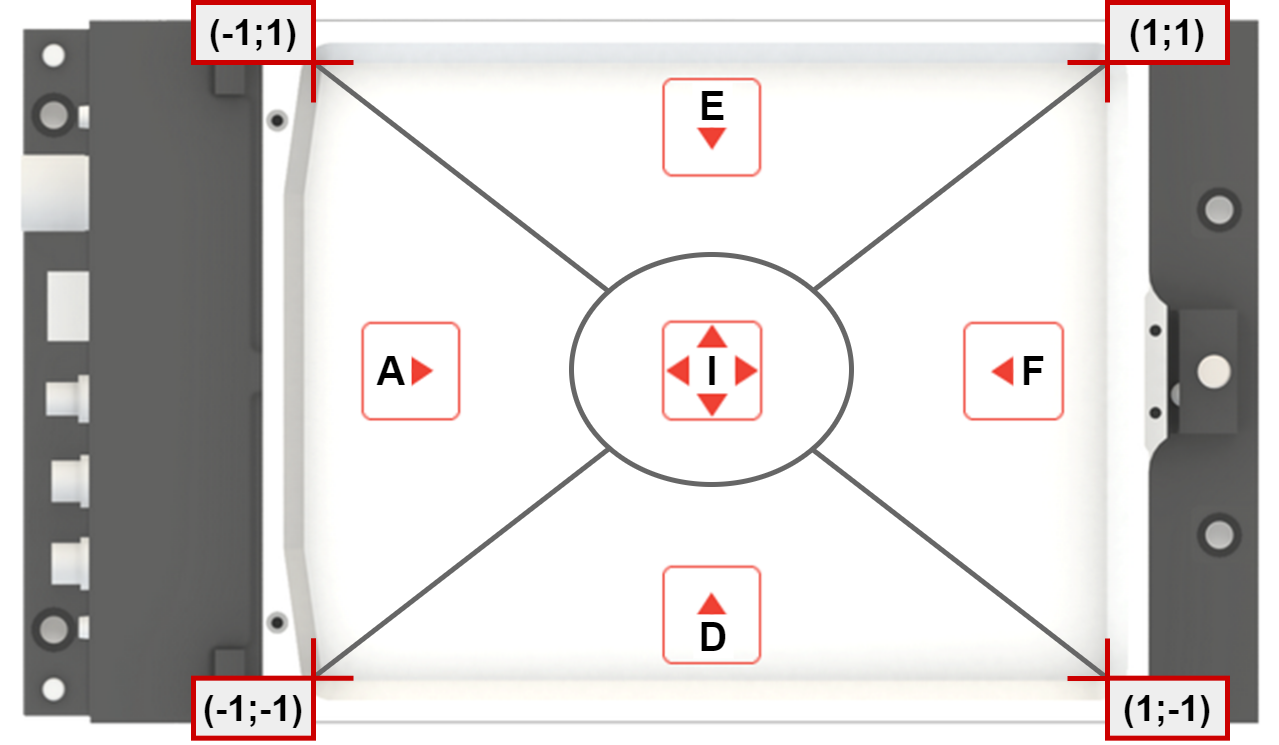
Fig. 118 Platform division for smart centering
Duration of vibration for smart centering
The calculation of the smart centering duration is explained with the example of Fig. 119. The center of mass (0.2;0.5) is located in the portion E of the platform. The execution of a Smart Centering EC will try to bring the center of mass of the parts to the middle of the platform using the vibration type E (Right). The duration is calculated based on the farthest coordinate \(d_1\) and the duration needed to cross the whole platform \(t(d_2)\) (see How to set the duration). In the example of Fig. 119, the farthest coordinate is \(Y=0.5\).
The formula below is then used to compute the duration \(t(d_1)\).
assuming \(t(d_2)\) set to 1500 ms and \(d_2=2\).
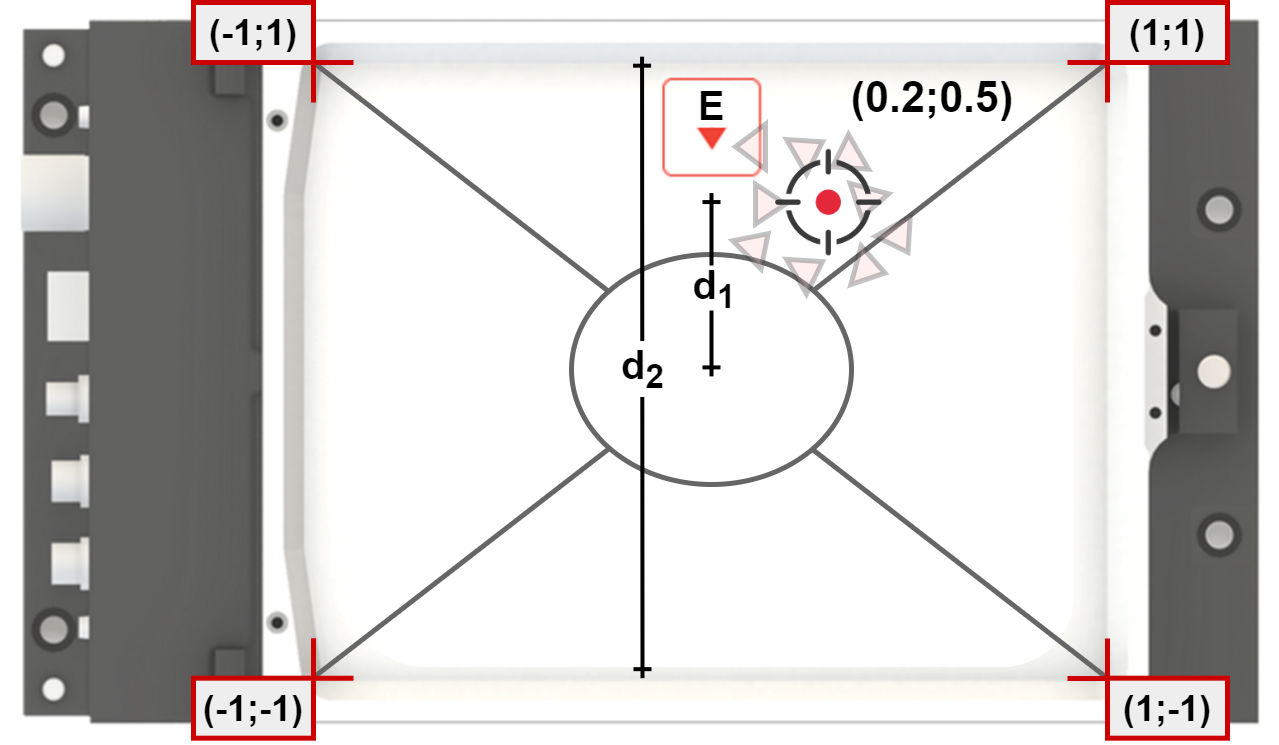
Fig. 119 Duration of a Smart Centering action
Number of parts for smart feeding
When using a smart feeding action EF or a sequence ES that includes a smart feeding action, the number of parts and the optimal number of parts on the platform must be filled in. These parameters will be used by the Asycube to automatically adjust the vibration duration of the hopper. The more parts there are on the platform, the shorter the vibration time. When the optimal number of parts on the platform is reached, the vibration decreases to zero. In between, the vibration duration is linearly interpolated. Refer to Smart Feeding for more information or to smart feeding examples for concrete examples.